
The 100K & 120K houses designed by Interface Studio Architects for Postgreen Homes, sit on a corner in the East Kensington neighborhood of Philadelphia. Photo: Sam Oberter/Sam Oberter Photography
Location | Philadelphia, Pennsylvania, USA |
Date | 2008-9 |
Developer | Postgreen Homes |
End User | 10 households |
Design Firm | Interface Studio Architects |
Structural Engineer | Larsen and Landis |
Contractor | Manor Hill Construction |
Additional Consultants | MaGrann Associates (LEED) |
Funding | Bank financed |
Total units built | 10 houses |
Cost per unit | $100 000-$120 000 USD |
Area | 106 sq m/ 1150 sq ft |
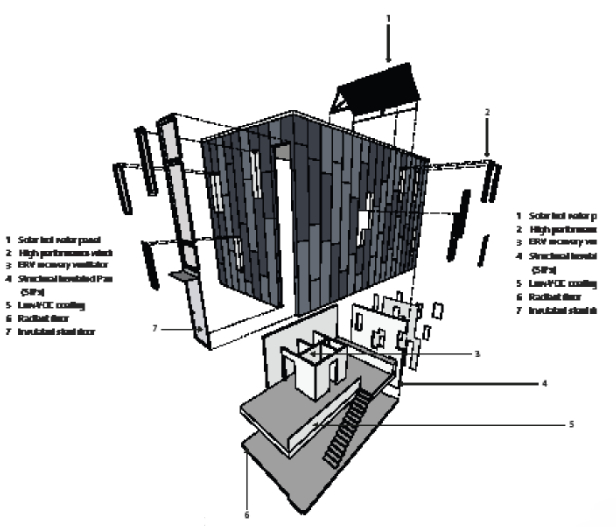
An exploded axonometric of the sustainable features Interface Studio Architects, LLC
A lot of architects talk about the benefits of mass customization but few are doing it. Prefabricated home building allows buyers to choose customized options from a kit of parts. Most of these homes, with the exception of the mobile home, remain in the domain of wealthy clients and architects seeking to push the boundaries of building delivery methods. Prefab homes are typically more expensive than their traditionally built counterparts of the same size and quality. Postgreen Homes and Interface Studio Architects teamed up to address this challenge with the LEED Platinum-certified 100K House, a single-family prefab house built for $100 000.
Postgreen, a real estate development company started by husband and wife Chad and Courtney Ludeman, created an online customization tool to make the process of designing a home much like that of configuring a new laptop. Buyers can choose a home model and specify everything from countertops and floors to ceiling fans and appliances. Chief Marketing Officer Nic Darling attributes their large following to social media.
The homes are LEED certified, which requires demonstrating leadership in energy and environment designs and involves documenting design and construction decisions from beginning to end with the US Green Building Council. The green consulting firm MaGrann Associates worked with the 100K House team in Philadelphia, Pennsylvania, to verify that the home satisfies the LEED certification checklist. Items on the list include cutting back use of energy, water and gas; reducing construction waste; and using sustainable materials throughout the home.
Postgreen and Interface Studio Architects started small in the first two years of their collaboration, initially constructing the 100K House and then the slightly larger 120K House. Production ramped up and they completed five additional houses in 2010. Three of those houses incorporate solar PV panels and the others were built to the German Passive House standard. The first four houses were built with Structurally Insulated Panels, which are prefab components that were manufactured in a Pittsburgh, Pennsylvania, factory. Their benefits include less material waste, higher wall insulation values, and quick, onsite assembly.
The goal for 2011 was to complete 50 new units. However, they decided to make the shift from prefab to a set of standardized stick-frame construction details. They came to the realization that tract housing was less expensive and dropped prefab. Their decision was due in part to the availability of low-cost labor created by the recession which began in 2009. “This choice was driven by ease of construction, particularly in an urban environment,” Darling says. “Our current strategies get the same or better results with less difficulty.” Additionally, the move away from prefab makes it easier for them to expand outside of Philadelphia because they won’t have to secure a new manufacturer. “While our wall assemblies and details are unorthodox, they use basic construction techniques which are very familiar to crews all over the country,” Darling says. Postgreen Homes is now building the houses themselves through their affiliated company Hybrid Construction.


left image: “There seemed to be a market for design savvy homes that are energy efficient at a reasonable price point,” said Chad Ludeman, founder of Postgreen Homes. Sam Oberter Photography, LLC
right image: The Ludeman family in the 100k home. Sam Oberter Photography, LLC
“There is one home in particular that we will claim we sold on Twitter.”
Nic Darling, Postgreen Homes chief marketing officer
READ OR LEAVE A COMMENT