Location | YangLiu Village, Sichuan Province, China |
Date | 2008-9 |
End User | 400 earthquake survivors in Yang Liu Village |
Client | Chinese government |
Design Firm | Rural Architecture Studio |
Design Team | Mei Fan, Tsing Hua, Jiang Jiaije, Liang Jin, Ma Maolin, Huang Yabin, Hsieh Ying-Chun |
Engineering | Hsieh Ying-Chun, Autodesk-China |
Contractor | Autodesk-China, Local villagers, Hsieh Ying-Chun |
Manufacturer | Rural Architecture Studio |
Consultants | Luo Jiade (Tsinghua University sociology department) |
Funders | Autodesk; Beijing Red Cross Foundation; Narada Foundation; Hsieh Ying-Chun |
Cost per unit | 90 000 Chinese yuan/$13 770 USD |
Area | 108 sq m/1162 sq ft |
Number of units | 56 units |

Roofs are built from corrugated steel and walls from cement. Insulation consists of readily available local materials such as bamboo, wood, stone, straw, and earth, minimizing construction and transportation costs. Photo: Rural Architecture Studio
China and Taiwan are in a region with complex tectonic geography and seismic activity. In the fall of 1999, a 7.6-magnitude earthquake struck Taiwan, destroying the stacked brick and stone buildings common to the country’s rural areas. Thousands of people died and many were displaced. The widespread devastation created an immediate need for housing.
Among the first to respond was Taiwanese architect Hsieh Ying-Chun. He realized the need for quick, resilient housing that could be erected by people who did not have specific training—a departure from the traditional chuan-dou wood frame construction used for over 5000 years. Ying-Chun turned to preformed steel beams as a solution. “Lightweight steel helps to create the openness for my building system and can be applied to different sorts of houses,” Ying-Chun says.
When an equally catastrophic earthquake hit China’s Sichuan province in 2008, the software company Autodesk teamed with Tsinghua University and Ying-Chun to create the Ma’erkang Project. Using 3-D design and engineering rendering technologies and Ying-Chun’s steel frame design, the team created a disaster response plan focused on providing a blueprint for permanent, sustainable, replicable rebuilding on a large scale.
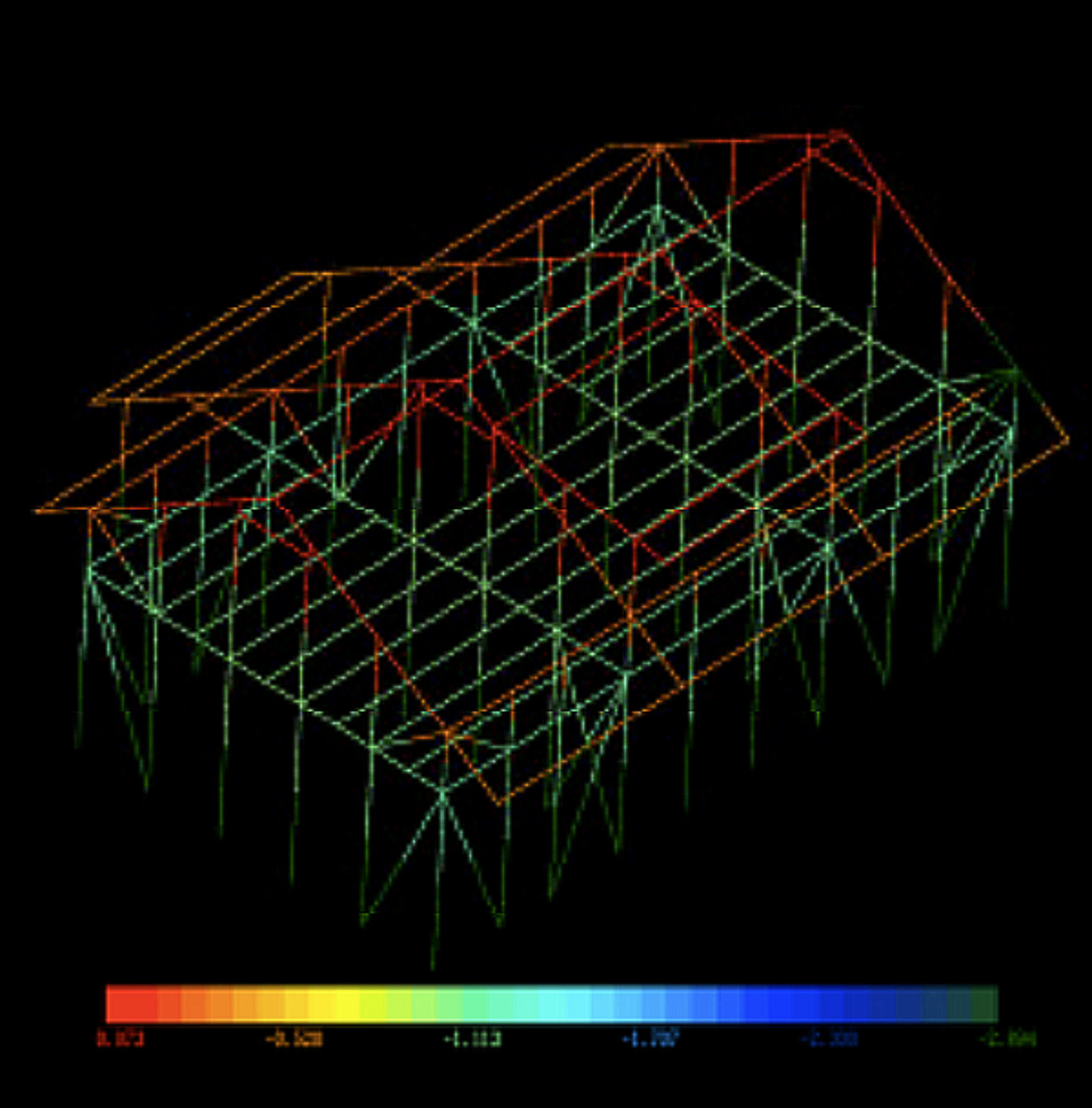
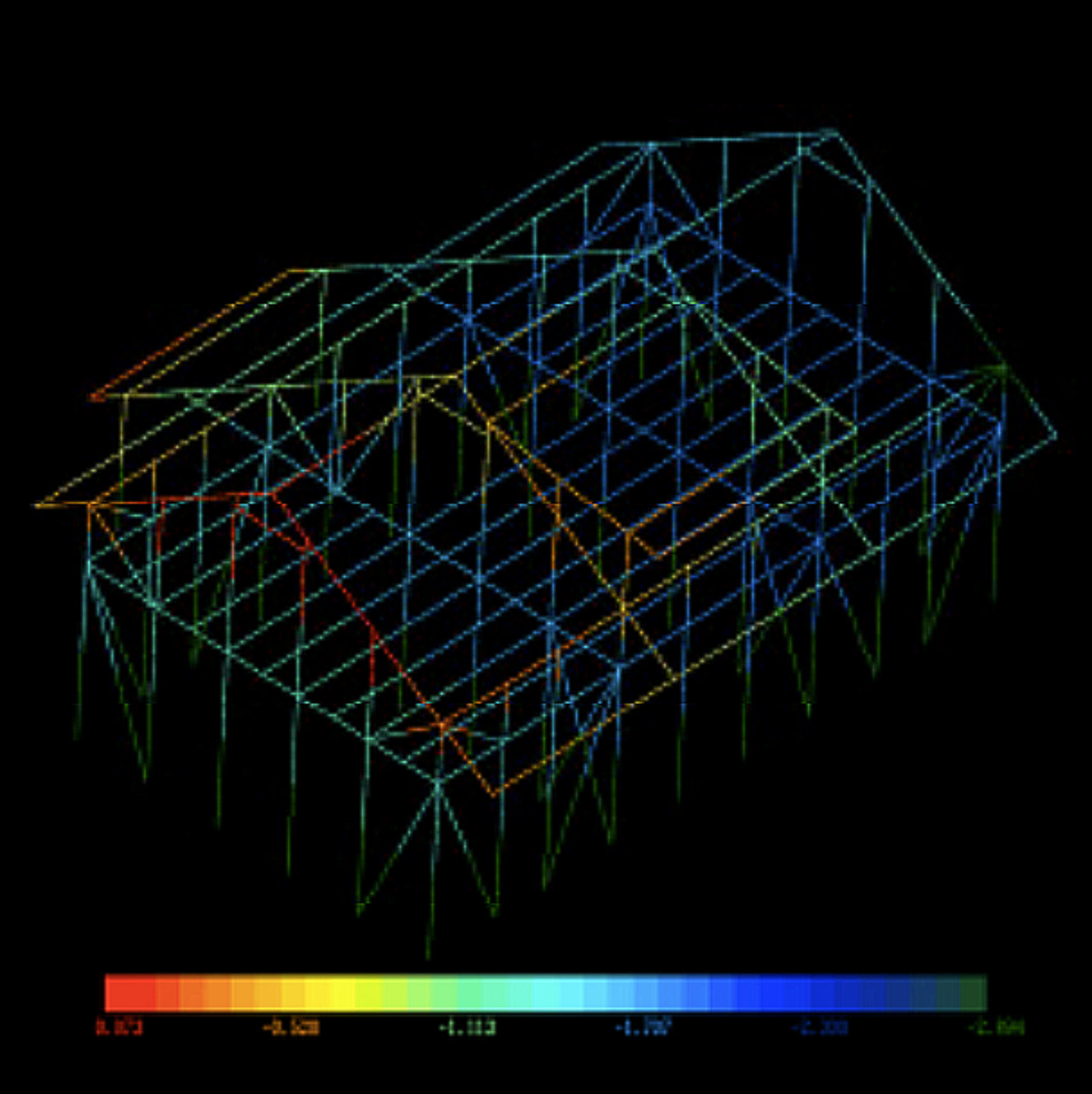
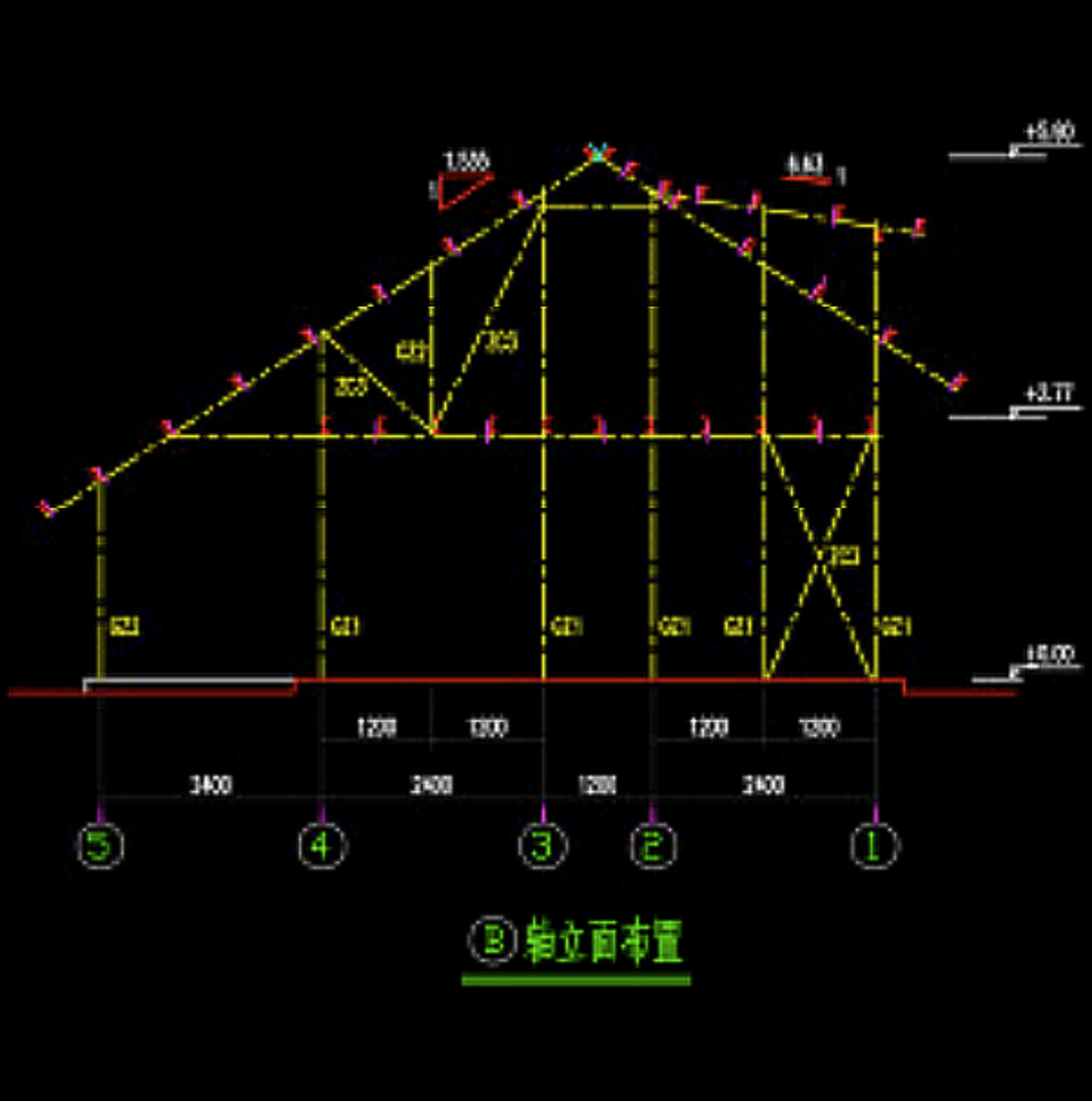
The Autodesk Research and Development team in Shanghai ran a load analysis on the steel frame design through structural simulations to help ensure maximum stability and earthquake resistance. Image: Autodesk
In order to ensure maximum stability and earthquake resistance, the Autodesk research and development team in Shanghai, China ran Ying-Chun’s design through rigorous structural simulations, according to Autodesk spokeswoman Roohi Saeed. In addition, analysis visualization modeling of sun, shade and wind conditions showed the thermal activity of the house year-round. “Using Autodesk Revit Architecture software, the team analyzed energy savings and ultimately designed a 50 percent energy-efficient building that performs well in summer and winter in different climatic conditions,” Saeed said. Detailed reports of materials and construction costs were calculated to reduce waste. The team also did data output on the carbon emissions of product production and construction to understand and reduce their carbon footprint for the project. Within 9 months, a team of designers had produced five standardized home designs that could be configured in multiple ways.
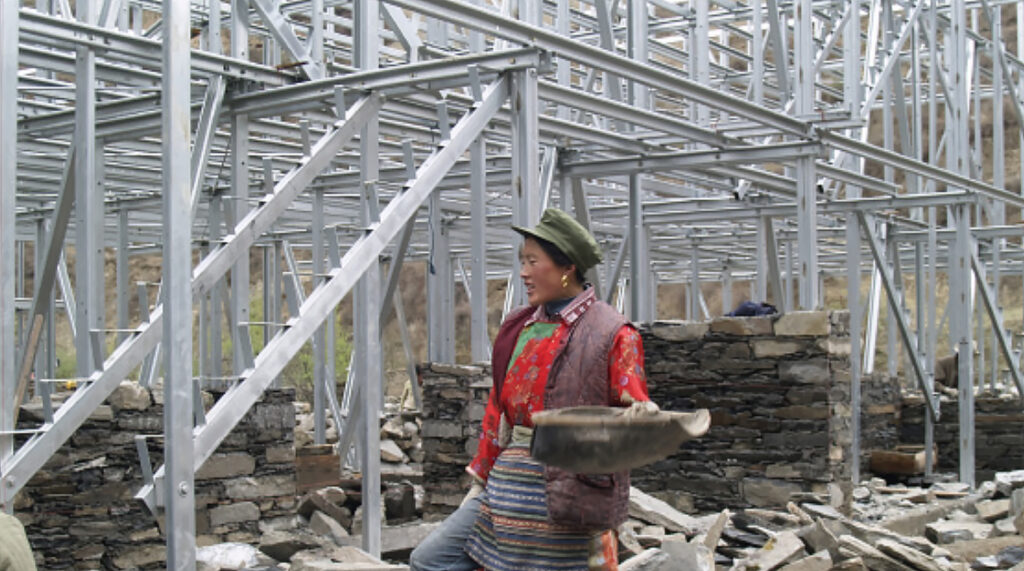
A earthquake survivor surveys the reconstruction efforts in Yang Liu. Steel beams can be bolted together into easily configured forms. Photo: Rural Architecture Studio
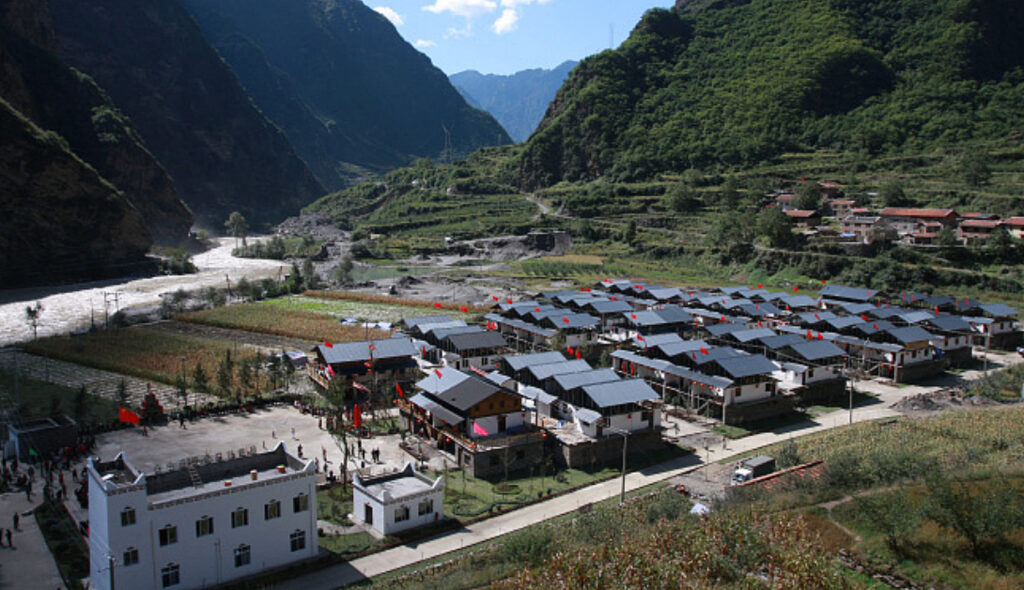
Ying-Chun continues to help with disaster reconstruction. Since the Ma’erkang Project, his firm Rural Architecture Studio has helped organize labor and financing so that the steel frame design can be built independently. Photo: Autodesk
READ OR LEAVE A COMMENT