Featured Project | Da Mor Lee School |
Location | Pingtung County, Taiwan |
Date | 2009 |
End User | John Lamorie and Shelly Wu and 50 students |
Client | Da Mor Lee School |
Design Team/Contractor | John Lamorie, Shelly Wu |
Funder | Self-funded |
Cost | $248 000 New Taiwan dollars/$8602 USD |
Area | 75 sq m/807 sq ft |

Completed Wastepaper School made from more than 1300 bricks. Photo: John Lamorie
John Lamorie is one of the only foreigners in rural Pingtung County, Taiwan, where large gravel companies and family betel nut farms occupy most of the land. Locals were understandably curious and word spread quickly when, in 2009, he began building a small home and English school out of recycled newspaper. “Before we were even finished, we had people coming up, trying to poke holes in the blocks, saying, ‘Is this really paper?” he recalls.
A former professional building inspector, Lamorie was well qualified to tackle the trial-and-error aspects of building with papercrete, a mixture of paper, water and concrete used in ways similar to adobe. Papercrete has been around since at least the 1920s but is not widely used. Though labor-intensive, it recycles waste material, has excellent insulating properties, and is inexpensive and strong. With reinforcing and waterproofing, it is ideal for the tropical southern Taiwan.
Lamorie and his Taiwanese wife, Shelly Wu, a yoga instructor and fellow English teacher, designed the building themselves and recruited their students to collect over 1400 kilograms (3086 lb) of paper. “We have a reward system for the school, little tokens that students can redeem at a local shop, so we just extended that,“ Lamorie says. “We got paper every couple days, nicely bundled and weighed.”
Lamorie made 1300 papercrete blocks to form the walls, plus additional batches for mortar and plaster. He fabricated a papercrete mixer to combine the water, newspaper and cement, out of a lawnmower blade and a 500-liter plastic water tank. A pickup truck bed was the base for the trailer. Lamorie welded the lawnmower blade inside the tank to the driveshaft of his car, so as he drove down along local roads, the trailer being towed behind mixed the papercrete. When combined, the papercrete was poured into rectangular molds 15 x 15 x 40 centimeters in size. Boric acid and borax are combined to the mixture to make it fire resistant. They were moved after 24 hours, then dried for several weeks to several months depending on the weather.
The papercrete blocks were easy to stack within the building’s post-and-beam structure and could be cut to fit with only a handsaw. Concrete nails and reinforcing steel bars were inserted into the blocks for typhoon and earthquake resistance.
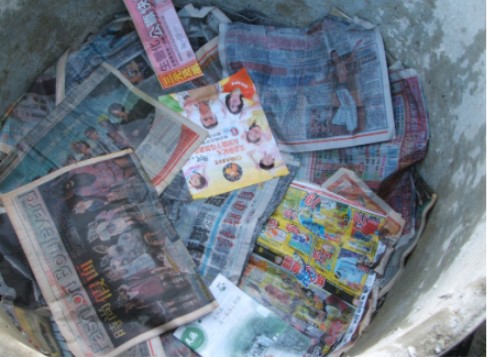
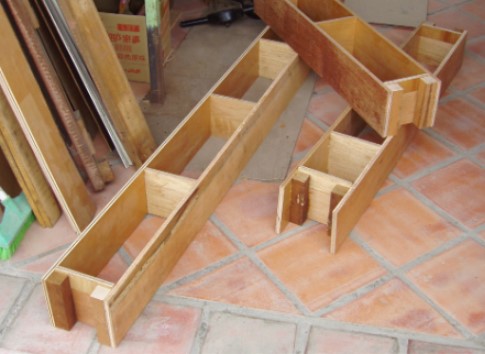
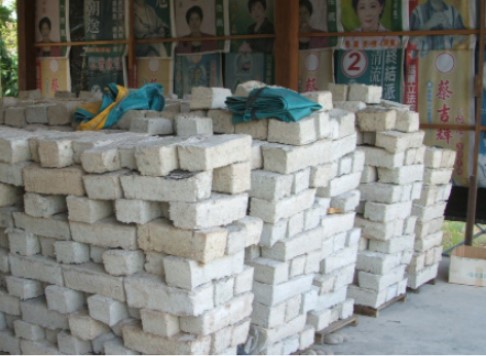
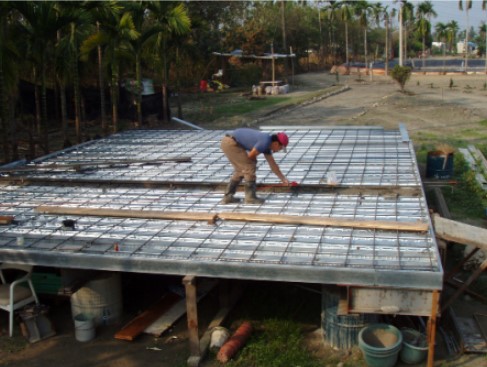
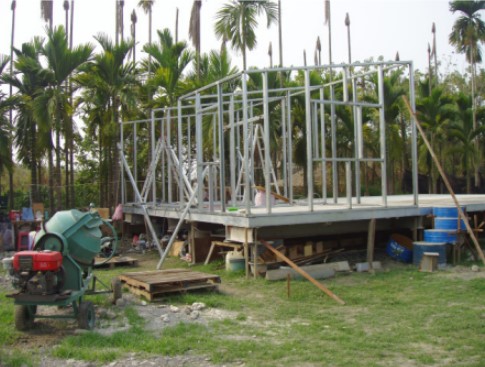
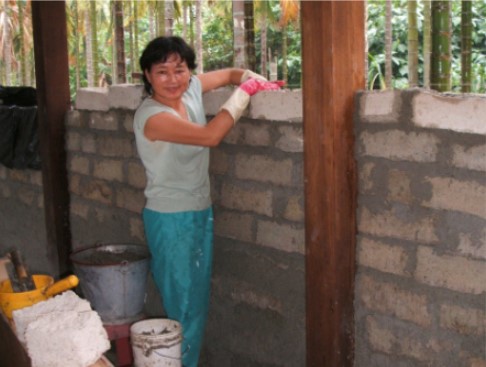

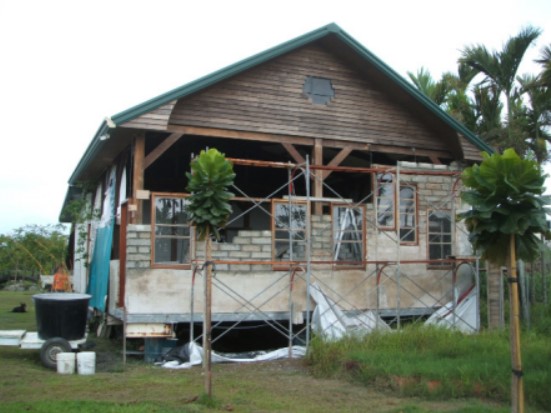

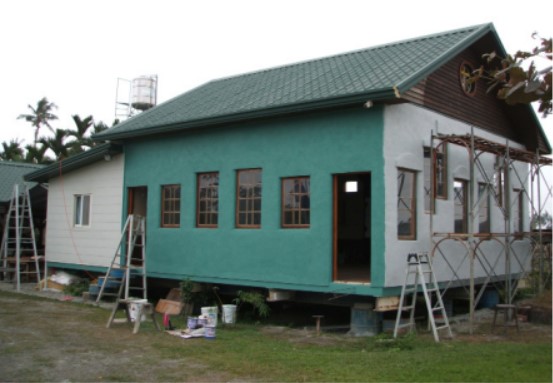
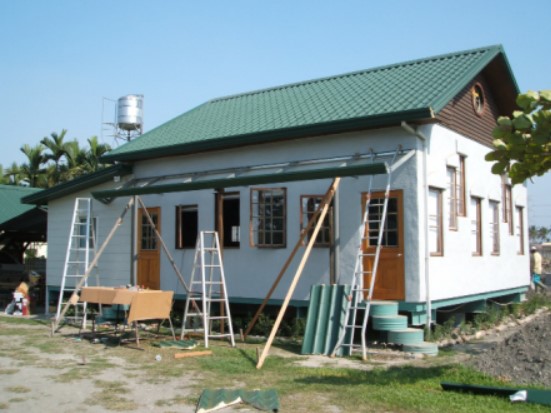
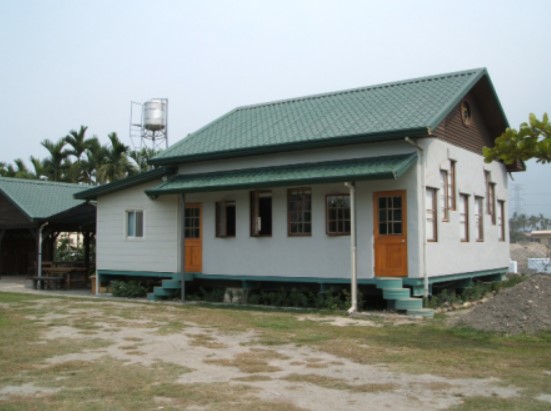
Series of photos show making of the Wastepaper School from start to finish. Photos: John Lamorie
READ OR LEAVE A COMMENT