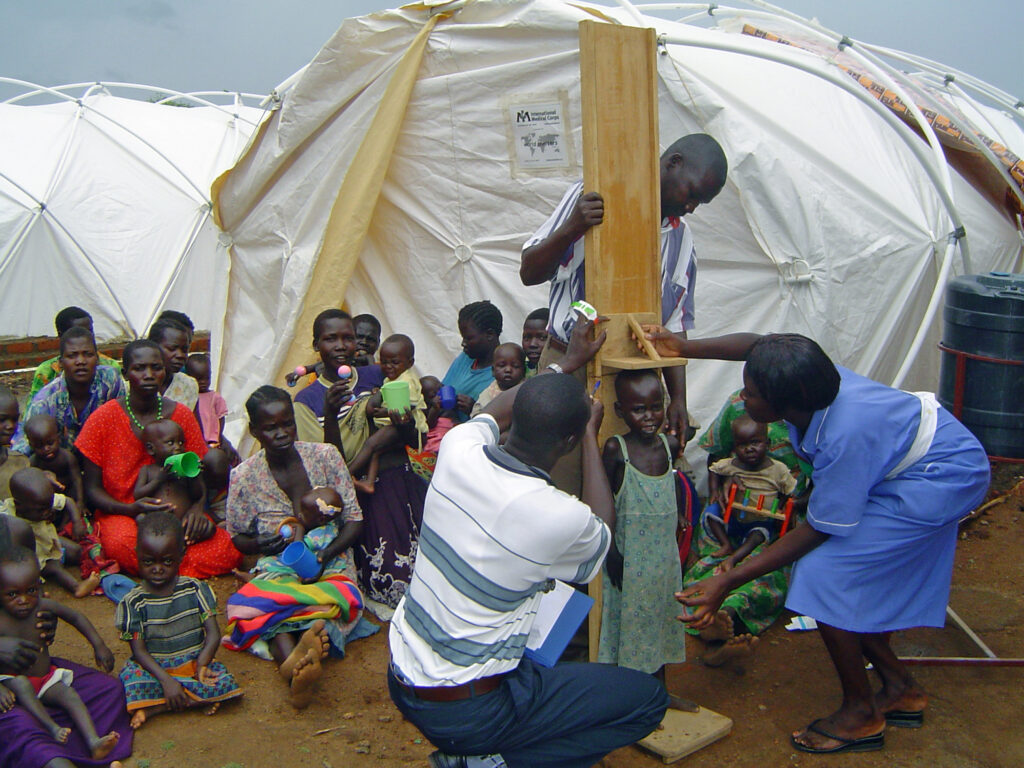
A health clinic set up by the nonprofit International Medical Corps in Uganda using the Shelter Frame Kit. World Shelters
Location | Various |
Date | 1983–present |
Organization | World Shelters |
End Client | Displaced populations, emergency field operations |
Design Team | Steven Elias, Bruce LeBel |
Project Partner | Buckminster Fuller Institute |
Cost per unit | $365 |
Area | 269 sq. ft./25 sq. m |
Occupancy | 6–8 people |
Dimensions | 24 x 11 x 8 ft./7.4 x 3.4 x 2.6 m |
Packed Dimensions | 15 x 15 x 60 in./38 x 38 x 152 cm |
Weight | 66 lb./30 kg |
Interview
Bruce LeBel World Shelters
Many designers have commented on the difficulty of breaking into the relief “industry.”
Underfunded, overworked aid organizations are often unwilling to take chances with new designs. In their defense not a month goes by that the major aid organizations aren’t besieged by some designer somewhere offering the latest panacea to the world’s housing crisis. As one aid worker deadpanned, “Sometimes enthusiasm overtakes experience.”
For Bruce LeBel, however, experience has never been an issue. In this interview conducted in March 2005, he talks about the inspiration behind his and his partner Steven Elias’s Shelter Frame Kit, their struggle to bring it to market, and, ultimately, their decision to produce and distribute the design through their own nonprofit, World Shelters.
How did you first get involved in providing humanitarian aid?
I started out as a high-school science teacher. I did my first disaster-relief project in 1976 in Guatemala after the earthquake there. I was part of a group from the Mohawk Nation that worked in small villages that hadn’t received aid from other sources. The unreinforced adobe-block walls and tile roofs were what had collapsed and caused most of the death and injury in the villages. CARE had a program offering roofing material for anyone who could get up walls. So what I developed was a combination of Japanese and Mexican traditional building techniques. Instead of thick adobe blocks, we used posts and woven-bamboo lattice with adobe applied as stucco. Then, in 1977, I did a graduate tutorial with Bucky Fuller.
That must have been interesting. What was it like working with Bucky?
He was someone you could spend an hour with and then have a month’s worth of work to do. He had an amazing way of asking the salient question. I think that was the key for me. It was just the way he would take the work I was doing and ask the salient question that would take me to the next level. I had a twofold program with him, one part of which was developing design science curriculums for high schools. The other was structural design with an emphasis on tensegrity, tensile structures.
When I finished my program with Fuller, my wife and I moved to Berkeley, and I went to work for The North Face, which was the first company that used Fuller’s principles of “tensegrity” in backpacking tents. Bob Gillis, together with Bruce Hamilton of The North Face, developed the first flex-wand backpackin tent. That’s the basic technology that we still use for our disaster relief shelter. We still buy clips from Bob [see “GripClips”].
How did the Shelter Frame Kit come into being? Was it something you started while you were at The North Face?
A colleague I had known through work with Fuller, Steven Elias, also had experience doing disaster relief work. He had a little business called Icosa Domes. (Note: Unrelated to Icosa Village, Inc.) The OFDA [Office of Foreign Disaster Assistance, a division of the United States Agency for International Development (USAID)] had used Icosa Domes in Guatemala, Iran, and Beirut before realizing the hard part is the logistics. And doing something that was as heavy and bulky as the cardboard Icosa Dome just didn’t work logistically for relief work. The shipping and in-country handling was too difficult.
After Fuller died in ’83, Steven and I got together and said, “We really ought to just do something. There’s a legacy here. Let’s focus on developing a lightweight, human-transportable, flame- retardant, durable shelter.” So we started Dymax and began working on product design.
How did you come up with the idea of using standard relief plastic sheeting rather than supplying your own covering?
It was a phone call. We were exploring a range of different sheeting materials and decided that USAID would probably be a good contact, and we should find out what they use. We then found there was a fellow named Roy Limpitlaw, this would have been in 1984, who had done a study and a write-up for USAID on temporary shelters. This was right at the time that Fred Cuny was starting to get going, too. He put us in contact with the supplier [that] developed the specifications for the USAID sheeting material. When we found out about this material, we brought in samples and started making shelters with it. Then, when we found that USAID was distributing this to disaster sites, we thought, well, this is just real clear. Not only is it an excellent material, but it’s already there. What we really need is a design that will operate as a shelter frame kit without the sheeting material and have it made in the field with the sheeting that’s there. That’s the seed for our work, this extraordinary sheeting material that shows up after every disaster. We hired Roy as our sales rep, and Roy was able to make the contacts and pull the strings and get an appointment for us with OFDA. We brought in our demo shelter and demonstrated it to the program manager and to the procurement manager and the logistics officer…. And, here we are out on the front lawn of the State Department setting this thing up, and they are sort of gnashing their teeth because here are these young turks from California with this idea. And then the director of OFDA comes down while were just about to set this thing up, and it just went up so fast. It was beautiful the way it went up. And the director says, “We really need to include this shelter in the evaluation that we’re doing.” So there we were, and all of a sudden we were in OFDA’s first national competition for emergency shelter.
“Then, we had lunch with Fast Eddy. He saw what we were doing and how dialed it was. He said, ‘Tomorrow we are going to meet at my office. I am only going to take 20 percent off the top. I’ve got all the channels worked out, and here is how it’s protected.’ We looked at each other and said, ‘We cannot go to this meeting. Time to get out of the country.’”
Bruce LeBel, World Shelters
What was the competition all about? Were they testing different designs?
They were doing a competition to procure tent supplies for various relief operations. After winnowing down the entries and going through a bidding process, they decided to do a field test in El Salvador and Guam and other areas. So now we’re in the national competition for going globally, and after going through various filters, there were two products left: ours and one from an outdoor equipment company. The first test site was El Salvador, back in 1985, after the earthquake there. They brought in 50 of our shelters to different distribution centers. So we get the call from USAID about this, and we say, “Well, who is going to be the evaluator?” And the fellow who they designated to be the evaluator was the sales rep from the outdoor equipment company. So, we thought, “This is interesting. Tell you what, we are going to go to El Salvador just to watch.” It was a huge mistake because we were essentially calling them on their conflict of interest.
We get to El Salvador and it takes a week for the stuff to get through customs. Frankly, I think they were waiting for us to run out of patience and leave. We spend some time with the evaluator, who actually ends up writing some objective reports. And we take some photographs of how the plastic sheeting on its own was being used, which for the most part was nothing more than using it as a lean-to, or draping it over walls or roofs that had holes in it. They’d hang it between trees. It was just draped. There was absolutely no structure to it at all. So it very much reinforced the validity of the concept behind the Shelter Frame Kit.
How did the test go? What was the response to your design?
We learned quite a bit from that experience. During the time we had available while the shelters were clearing customs, we were following the trail of where aid money goes and discovering how little of it gets used for aid and how much of it gets siphoned off. It was really extraordinary to see where so much of the money was going. Basically, the military power structure was siphoning it out and getting the money out of the country.
We met this fellow, Fast Eddy, who was very well connected, very high up. We were given his name by the American Chamber of Commerce, and after we had lunch with this fellow, after being there seven to eight days and having put together a whole scenario for financing redevelopment with low-tech walls and getting the bank and the tractors and the land brokering all ready—I mean, it only took us a week, and we already had this redevelopment scenario worked out—then, we had lunch with Fast Eddy. He saw what we were doing and how dialed it was. He said, “Tomorrow we are going to meet at my office. I am only going to take 20 percent off the top. I’ve got all the channels worked out, and here is how it’s protected.” We looked at each other and said, “We cannot go to this meeting. Time to get out of the country.” And we left. And that was it. Never did see one of our structures go up. So we learned an extraordinary amount, but it wasn’t about what you think.
What about the bid with OFDA?
We followed the test and just kept things on hold for production. We got reports back that they weren’t able to perfect the other tent design, and our tent went up like a dream. We won the competition, but unfortunately then the feedback from OFDA was ”Our budgets have been cut. We are not going to be buying any of these tents that we thought we were going to be buying thousands of.” And the same scenario repeated itself 15 years later.
What happened in the meantime?
They were used in Guam and Mozambique as part of the first OFDA test, and then we continued working with relief organizations and developing contacts, but we were just never successful breaking in.
Why do you think that is?
The big problem with shelter is that the logistical issues and the cultural issues totally overwhelm the designs. In particular, land is a big problem. Once people are living someplace, they aren’t going to move unless they’ve got somewhere else to go. So, the ideal solution is one that will perform perfectly for six months and the next day turn into dust. Ours lasts two years.
The geometry, the dimensions, the materials are only a small part of the total package. To me, it’s really not only having an ability to solve the logistical problems but also being able to maximize the use of locally available materials and labor. You can make World Shelters shipping in nothing more than what I refer to as “user-friendly live ware.” All you need is to ship in one of our associates, and as long as there is cord, sheeting, and some kind of pole material, we can produce self-supporting structures.
How did you eventually get the kit into the field? Where was it finally used?
In the end it was back-burnered for seven or eight years, and then we got a call from the group that was doing the next test for OFDA. Once again there was a set of specifications and a test process and a commitment that they would be purchasing X number of units. The upshot was they turned around and said—just as happened in the previous go around—”Thank you very much, wonderful product, our budgets have been cut.”
We started getting smart at that point. Even though my partner Steve and I are dyed-in-the-wool entrepreneurs, we realized: You know, we should start looking at this as a nonprofit. Because trying to sell to the government is a 50-year task. It’s not a five-year task or a 10-year task. One day it will happen, but we can’t bank on it. So we thought, how do we get it to the NGOs, when shelter is nobody’s main mission and everybody’s scrambling, and we thought, well, we should approach it as a nonprofit ourselves.
In 2002 we started working with the Buckminster Fuller Institute. Through some joint fundraising, we were able to get units out to IMC [International Medical Corps], which used them as temporary clinics, to the Jordanian Red Crescent, which put some units along the border of Iraq, and to the Mexican Red Cross. A German agency also used them in Kosovo for redevelopment activities. They were used as housing for
people who were doing construction and as temporary shelters for people until they could move into their new homes.
How much did you raise and how many shelters were you able to produce?
We raised about $20,000 to $25,000, and with that we were able to produce and distribute about 50 25-square-meter [269-sq.-ft.] shelters—including shipping.
That’s the thing that so many people don’t realize. Shipping can be half the cost of manufacturing the units, if not more.
That’s one of the things that we’re working on right now. We’re trying to put together production facilities and warehouses, managing the logistics from start to finish.
The other really important part of design is not just having a product but having an organization, taking the responsibility to create an organization that is going to make it happen. All of the issues around designing and initiating and coordinating and building are handled by nonprofit organizations, and I’ve discovered them to be just critical.
Since we spoke with LeBel, World Shelters has gone on to provide emergency shelter to the Red Cross after Hurricane Katrina pounded the Gulf Coast of the United States, to International Medical Corps in Uganda, and in the tsunami-affected areas of Sri Lanka and Banda Aceh, Indonesia. It has also provided shelter in India (including the Andaman Islands), Venezuela, and El Salvador.
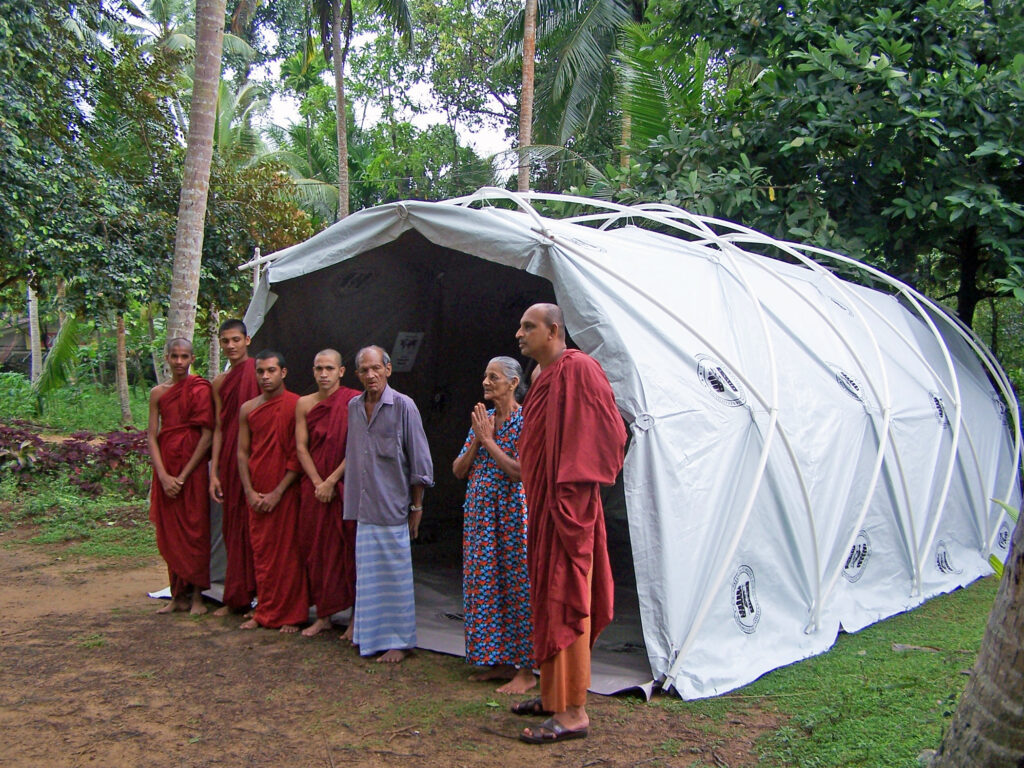
After the Indian Ocean tsunami of 2004, World Shelters’ structures were used by a monastery in Sri Lanka. The Shelter Frame Kit is intended to “turn sheeting into shelter.” The design takes advantage of the plastic sheeting supplied by the United Nations, USAID, and other agencies to disaster areas. The kit includes S-hooks, PVC pipe, cord, guy lines, anchor stakes, clips, connectors, and a pictorial instruction manual. World Shelters
READ OR LEAVE A COMMENT